MMA (Manual Metal Arc) welding with a coated electrode, is a type of welding widely used for its versatility and wide range of applications. Although it is used very frequently, there are still users who doubt about the type of electrode to choose or the polarity to use to achieve optimal welding. Therefore, throughout this article I will talk about the process and what are the types of electrodes that exist, their parts and the aspects that you should consider.
How does MMA welding work?
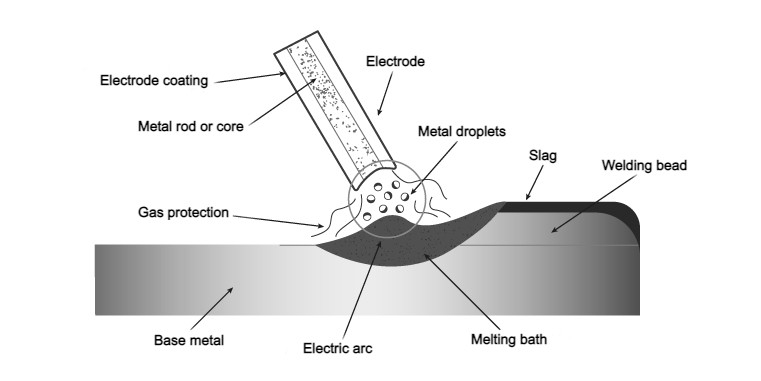
MMA (Manual Metal Arc) welding with a coated electrode, is a process by which metal parts are joined. Thanks to the heat emitted by the electric arc formed between the coated electrode and the metal base to be joined, the metal core of the electrode melts, filling and joining the pieces.
For this process to work successfully, it is important that you select certain parameters such as: a compatible electrode with the piece to be welded, the amperage according to the diameter of the electrode and the thickness of the piece, as well as the correct position of the terminals (direct polarity or reverse).
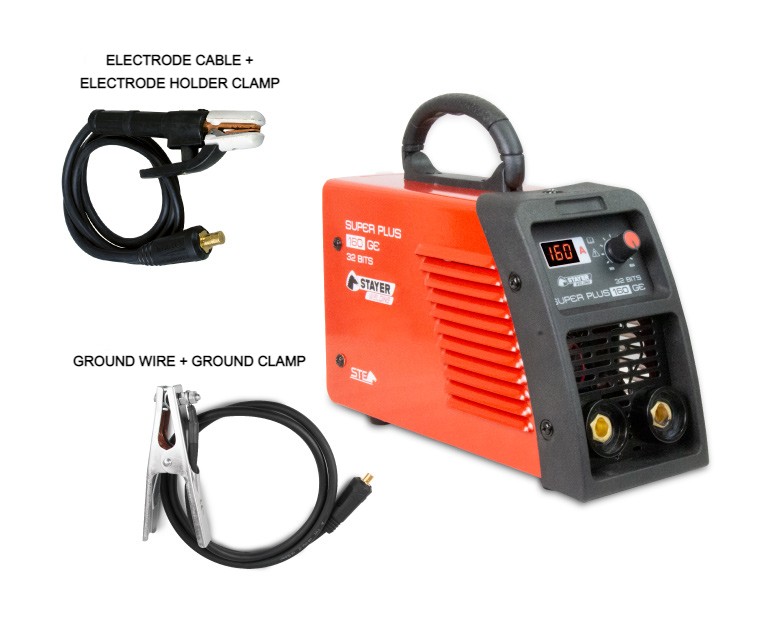
Let’s look at each of these points.
What does a coated electrode for MMA welding look like?
Electrode parts
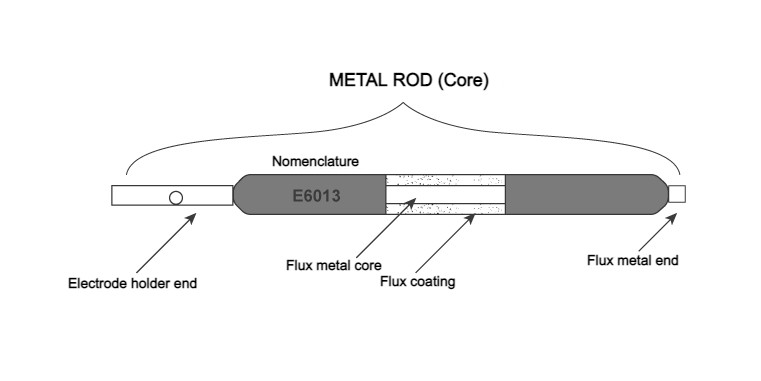
As you can see in the image above, the electrode has a metal rod or core, and a flux coating. At the left end of the rod is the electrode holder (uncoated metal area where the electrode holder clamp is connected), in the center is the flux core, and at the right end is the tip that will melt when welding (both parts are coated).
The molten coating forms a slag that protects the weld.
“How?” By preventing contamination of the molten material, improving and stabilizing arc priming, the finish, and the mechanical characteristics, as well as reducing the cooling rate and making it possible for the weld to be made in various positions.
“Do all the electrodes have the same components?”
I’ll tell you no. Depending on the material that you are going to weld and the kind of coating they have there is one type or another.
Types and characteristics of electrodes
According to the American Welding Society (AWS) and the American Society Mechanical Engineers (ASME) there are: acid, rutile, cellulosic and basic electrodes. Let’s see what their characteristics are.
Acid electrodes
Acid electrodes are made of iron oxides, ferrous magnesium alloys and silicon.
They are characterized by a stable arc, high deoxidation and easy slag removal. Easy maintenance and, despite their low cost, the welding is of good resistance but with a risk of cracking.
Rutile electrodes
In the case of these electrodes, their composition is mostly rutile.
They have a stable arc and a simple arc ignition. The weld bead they leave is aesthetically better than others and is well preserved and, in addition, like the acid electrodes, the weld is resistant but with a risk of cracking.
Cellulosic electrodes
The composition of cellulosic electrodes is cellulose with magnesium and silicon.
They have high penetration, workability and produce little slag. However, it is true that the hydrogen content is somewhat high.
Basic electrodes
Basic electrodes are composed of iron oxides and ferrous alloys. They have a less stable and shorter arc, as well as a very low hydrogen input. They must be at a storage temperature of 30º to 150º because if their coating perceives humidity it can generate porosity. But welds with this type of electrodes are very resistant.
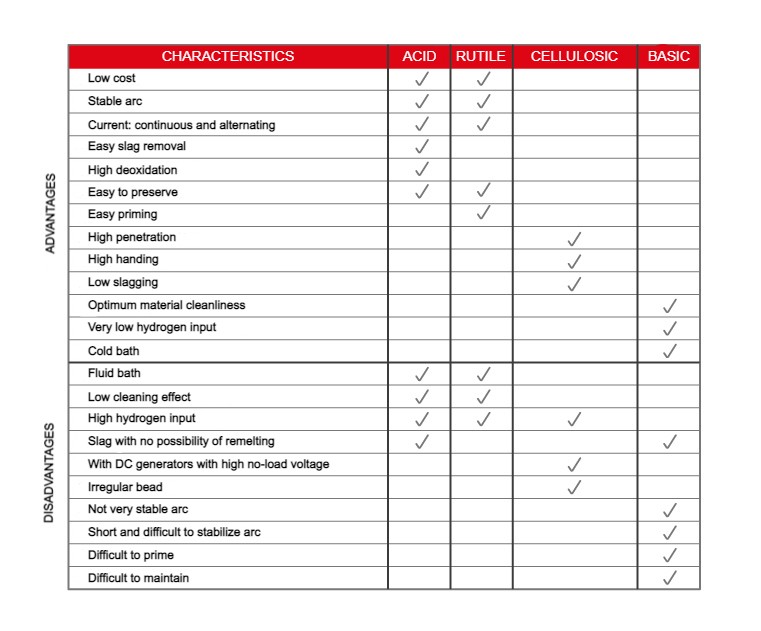
Electrode diameter
In general, the diameter of the electrodes is going to be conditioned by the amperage of the welding equipment that you use and the dimension of the material that you are going to weld. For your reference, here is a recommendation of the amperage range in which you should handle depending on the diameter of your electrode.
- 25-50 Amp for 1.6 mm electrodes.
- 40-80 Amp for 2.0 mm electrodes.
- 60-110 Amp for 2.5 mm electrodes.
- 80-140 Amp for 3.25 mm electrodes.
- 115-160 Amp for 4.0 mm electrodes.
- 160-210 Amp for 5,0 mm electrodes.
- 190-260 Amp for 6.0 mm electrodes.
Now that you know what types of electrodes there are, you may be wondering “What are they used for?”
What is each electrode used for in MMA welding?
Acid electrodes are used in construction for horizontal welding of low carbon steels with little presence of impurities.
However, rutile electrodes are used in boiler making, shipbuilding and metallic structures, among others, to weld, in all positions, small thicknesses of low-carbon steels with little presence of impurities.
On the other hand, cellulosic electrodes have high penetration and are therefore suitable for welding in all positions, including vertical downward, tubes, or where the bead on the reverse side is not possible or the electrode access is critical, of low carbon steels with little presence of impurities.
And finally, basic electrodes are suitable for welding in all positions, even with large thicknesses.
“And do all electrodes allow the same current?” Well, no. I will explain it below.
Types of current in MMA welding
Older welding equipment used alternating current at the output, so the current was not constant over time. However, today’s welding equipment, the Inverter, uses a full wave rectifier that transforms the frequency of 50-60 Hz from AC (Alternating Current) to DC (Direct Current), so that they can continuously weld long welding seams.
But for that to be possible, you must make sure that the electrodes are compatible with the current (direct or alternating) and polarity (direct or reverse). And the fourth digit of the AWS classification will be the one to indicate you (in the next section I will show you what it is).
In relation to the types of electrodes we have seen before, the connection that works best is:
- Rutile electrode: direct polarity.
- Cellulosic electrode: reverse polarity.
- Basic electrode: reverse polarity.
- Inox electrode: reverse polarity.
When the polarity is direct: the electrode holder clamp is connected to the negative pole and the ground clamp to the positive pole. When the polarity is reversed: the electrode holder clamp is connected to the positive pole and the ground clamp to the negative pole.
What is the meaning of the electrode nomenclature?
The electrodes have a standard nomenclature formed by a letter and four digits and their classification will depend on them.
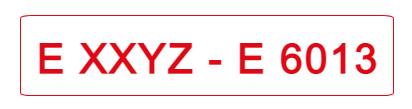
The letter E indicates that the electrode is suitable for manual electric welding.
The next two numbers XX indicate the minimum tensile strength, without heat treatment after the welding, of the deposited metal (measured in lbs/in2).
Letter Y shows the positions in which you can weld with that electrode. If it is 1, you can do it in flat, vertical, overhead and horizontal position; if it is 2 in flat and horizontal; and if it is 4 it is convenient to use it in flat position but also in vertical downward.
And the letter Z will be indicative of the type of current and polarity with which the electrode works best and the type of coating it has.
Therefore, what aspects must be considered before choosing an electrode?
- The metal base (material to be welded): its thickness and shape. It must be compatible with the electrode material.
- The type of current: direct or alternating.
- The electrical power.
- The position that allows the electrode.
- The resistance that supports the welding.
- Technical specifications required for the work.
- Efficiency and speed in the welding operation.